Lean Meetings
Meetings are necessary in all businesses, but by taking some guidance from systems thinking and Lean manufacturing, you can make sure you only hold those that are important and effective.
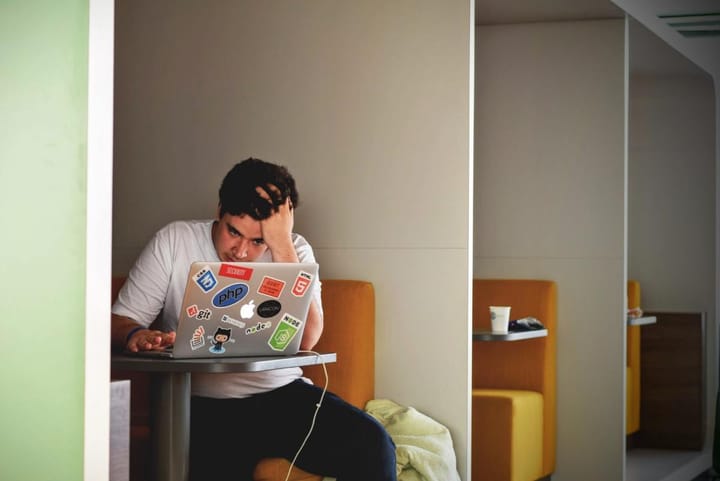
Photo by Tim Gouw
Ask anyone about the top three things that stand in their way of being the most productive and efficient they can be at work, and it’s almost guaranteed that meetings will make an appearance in that list.
One of the hallmark strategies for improving meetings is to prioritize their agendas. The agenda is, no doubt, an effective tool for clearly articulating what will be done in a meeting and can help discerning and savvy invitees determine if their attendance is actually required. However, meeting agendas are built upon one bold — and often erroneous — assumption: the meeting itself is necessary.
To begin to challenge that assumption, we must find a new framework for evaluating the importance and effectiveness of meetings. This is where we can leverage the philosophy behind systems thinking and Lean manufacturing.
Systems Thinking
A system is a set of related components that work together in a particular environment to perform whatever functions are required to achieve the system's objective. — Donella Meadows
Consider the larger “system” of how projects are executed and accomplished — all of the individual and group actions, processes, and people it takes to get stuff done. Even in the realm of “knowledge work,” raw materials (concepts, ideas) are transformed into a finished product. Undoubtedly, meetings will be part of that ecosystem.
If we consider meetings to be yet another component of “how we work,” we can start to assess their specific contribution to that system. Consider every meeting as having a series of inputs and outputs. Or, rather, outputs and inputs. And yes, the distinction in ordering is important.
Many companies have latched onto Value Stream Mapping as a great tool to analyze their processes (which it is). But when you look at their maps more closely, you often find that the production process is sketched in painful detail, whereas the information flow is barely suggested. — Michael Balle
Outputs
“What will this meeting produce, and are those artifacts valuable to the larger system?”
The foremost question to ask when setting up a meeting is: what will the meeting yield? Generally, outputs fall into three main categories: decisions, solutions, and knowledge. These categories, however, are not tangible artifacts. It is the responsibility of the meeting organizer to define ways of memorializing and socializing these outputs so they can be fed back into the system.
All too often, the outputs of a meeting remain in the shared consciousness of the meeting attendees, without deliberate action being taken to document or incorporate that data into future decisions. Asking the question “what or whom will be affected by the outcomes of this meeting?” can help inform the artifacts that need to be generated, whether that takes the form of an email recap, documentation, shared meeting notes, logged action items, etc.
Once meeting organizers have a clear picture of the outputs a meeting will produce, they can evaluate who or what is required to achieve them.
Inputs
“For this meeting to be effective and produce its desired outputs, what does it need?”
Definitionally speaking, the most obvious input to a meeting is people. Choosing the right people and setting the expectation of engagement is not always simple, however. Let’s look at this from the lens of the potential desired outputs:
- If decisions are to be made, the meeting organizer must ensure one or more individuals with decision-making authority are engaged in the conversation.
- If the meeting is being called to come up with solutions, the best attendees are those collaborative individuals wearing their problem-solving hats.
- If the purpose is to transfer knowledge (whether in the form of status reports, training, or anything else), the attendees should be those individuals who will benefit most from possessing that information at the end of the meeting.
Once the attendees have been identified, the next important input to the meeting is what context those individuals need for the meeting to be effective. This context can take many different forms, from a description in the meeting invite to documentation sent out as a “pre-read.” This context setting or generation can also take the form of individual conversations that need to happen to prepare for a meeting.
Once your systems thinking is done, so your outputs and inputs have been identified, it’s a short hop to actually visualizing what needs to come next, which is where Lean manufacturing comes in.
Lean Manufacturing
“If you always do what you always did, you’ll always get what you’ve always got.” — Henry Ford
The broadest definition of Lean manufacturing is the effort of analyzing the process to deliver a finished product. The core principle of this way of thinking is to eliminate waste in order to continually improve a process, constantly asking the question: where is there waste?
Lean manufacturing also involves continually asking whether a particular activity is directly creating value for the consumer. If we’re employing it in the context of meetings, however, we may consider “the consumer” to be meeting participants. Can we justify them being there? If not, their time is being wasted and they are not providing any value to the external consumer.
It’s important to remember that just like everything we do or propose, thoughtful execution comes down to introducing a change, testing and validating the results of that change, and feeding the lessons back into the system for iteration and further improvement. This means analyzing the process end-to-end, which is called a value stream. What does it take to go from an idea to a finished product? Many of those steps involve meetings that are an important part of the value stream—but unless carefully managed, those meetings have the potential to introduce a lot of waste.
Push vs. Pull
Something else we can take from Lean manufacturing pertinent to our analysis of meetings is its use of pull systems. That means the next phase of work only begins when the previous task is completed—something that protects certain stages in the value stream from producing more than the system can support.
In many cases, meetings are set on a predefined cadence in an attempt to keep these different parts of the value streams in sync and coordinated over a long period of time. In practice, though, these meetings are often reactive to the pace that different teams are working and attempt to reconcile these different schedules and work deliveries, which is the “push” model. Consider these two possible resulting scenarios:
- A meeting is regularly scheduled for every Monday, but tasks assigned the previous week are not yet completed. The meeting is held anyway, despite the fact that there are outstanding tasks—and possibly even more work is assigned.
- A meeting is regularly scheduled for every Monday, but tasks assigned the previous week are completed by Thursday. What’s going to be done on Friday?
An alternative would be using meetings to build pull systems in which outputs are intentional and clear and everyone understands the work and coordination necessary to take a work product from one step to the next. In the case of the scenarios noted above, for the first one, the meeting would not be held until all tasks previously assigned were completed, and for the second, the meeting could be held on Friday to get started on what comes next. Or, alternatively, if the mechanics of the handoffs were planned and shared in advance, a meeting could be avoided all together, as it does not serve to deliver knowledge, solutions, nor decisions to its attendees.
Moving Forward
Meetings are necessary in all businesses, but by taking some guidance from systems thinking and Lean manufacturing, you can make sure you only hold those that are important and effective. Meetings are synchronous. If there’s an efficient asynchronous, i.e., non-meeting way to translate inputs into outputs, do it.